Parts & Service Recommendations and Tips
Jan 09, 2019 . 1 min read
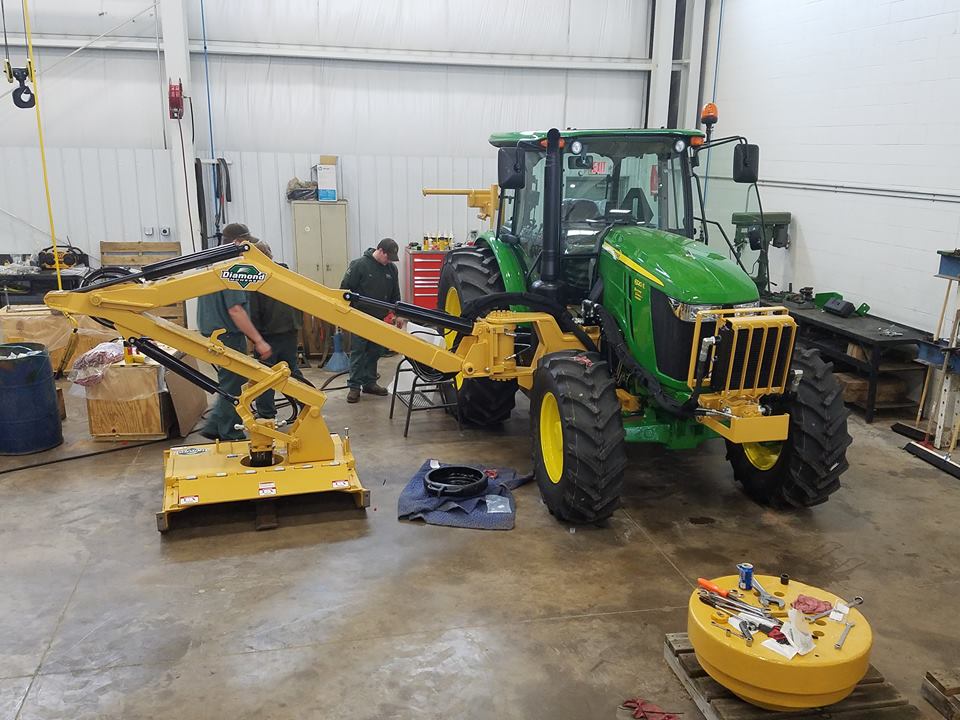
Equipment downtime is the bane of the vegetation management business. Below are some recommendations and tips to minimize downtime and maximize productivity.
Complete Daily Basics and Tasks
Daily maintenance is the number one most significant component of a machine's long-life span.
- Daily inspections will catch most problems and potential issues.
- Many manufacturers supply operating and maintenance manuals with daily maintenance schedules. These are great reference tools.
- Most equipment is marked with decals for critical or daily maintenance requirements to assist in maintaining the machine.
- Fluids and filters should be changed at their recommended intervals.
Make Sure Parts and Other High Use Items are On Hand During the Busy Season
Maintaining an adequate inventory of high use parts and components during the busy season is mandatory to reduce and minimize downtime.
- Filters and fluids
- Teeth, blades, knives, and other high wear items exposed to constant friction and erosion from the environment
- Bushings, seals, and bearings
- Belts, chains, and other driveline component
- Shields, covers, and similar safety device
Prepare for the Season
Certain times of the year can put extra demands on your machine and may require extra planning.
- Match fluids with viscosity to the anticipated temperature range at the operating site.
- Have fuels appropriate for your environment (for example: winter vs summer weather) on hand.
- Monitor coolant, oil temperatures, and levels closely.
- Keep cooling components like radiators and cooling fans clean and free of debris.
Don’t Attempt Machine Repairs If You are Not Properly Trained
Some repairs can be easily handled by the operator or maintenance crew; however, more complex equipment needs require trained service technicians.
- Many machines now have computers, modules, and sensors integrated into them, and more damage than good can occur if certain guidelines are not followed when conducting repairs.
- Usually the manufacturer and/or trained dealer service technicians have full access to diagnostic tools and specialized equipment. Take advantage of these assets to minimize downtime and additional costs associated with multiple repairs.
- Help out the dealer service technician. Take notes of unusual operating behaviors, sounds, what may have initiated or caused the problem, and relay this to your technician to assist them in diagnosing your equipment and speed its repairs.
Developing and maintaining proper and efficient habits helps keep routine maintenance simple, and will prevent downtime.
For common maintenance questions visit Tech Tips.